Stretch foil production process
Admin
3/9/20233 min read
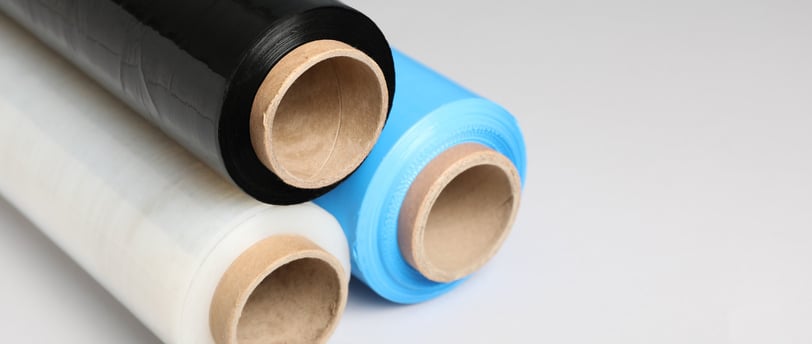
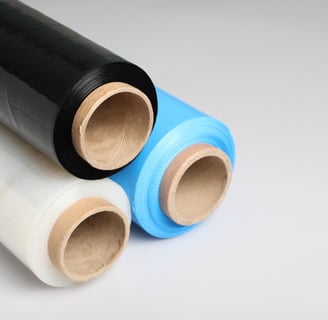
Vivopack® focuses on high quality. For the satisfaction of our clients, we know perfectly how important it is to provide stretch film with top features.
Stretch film production is a complex process that involves multiple steps and requires a high degree of precision and expertise. In this article, we will explore the various stages of stretch film production and the challenges in the production of high-quality stretch films.
Raw Materials
The first stage of stretch film production involves the selection of raw materials. Stretch films are typically made from a blend of linear low-density polyethylene (LLDPE) and other additives such as cling agents, slip agents, and UV stabilizers.
The quality of the raw materials is crucial to the performance and durability of the final product. The LLDPE used in stretch film production must have a consistent molecular weight distribution, as variations in the molecular weight can affect the film's strength, elasticity, and clarity.
Moreover, the selection of additives must be carefully controlled to ensure that the film's properties meet the required specifications. For example, cling agents must be added in the right quantities to ensure that the film adheres well to the product being wrapped, while slip agents must be added to reduce the film's coefficient of friction, making it easier to unwind and apply.
Extrusion
The next stage of stretch film production is extrusion, which involves the melting and extrusion of the raw materials into a thin film. The extrusion process is complex, involving multiple variables such as temperature, pressure, and cooling rates.
The raw materials are fed into an extruder, where they are melted and forced through a die to form a flat film. The film is then cooled and stretched to the desired thickness and width.
The extrusion process requires a high degree of precision, as even small variations in temperature, pressure, or cooling rates can affect the film's properties. Moreover, the stretching process must be carefully controlled to ensure that the film has the right level of elasticity and strength.
Winding
The final stage of stretch film production is winding, where the film is wound onto a core to form a roll. The winding process is critical to ensuring that the film is uniform and free from defects.
During winding, the film is stretched to its maximum elongation to remove any residual stresses that may have been introduced during extrusion. The film is then wound onto a core, with the tension and speed of winding carefully controlled to ensure that the film is wound evenly and tightly.
Challenges in Stretch Film Production
The complexity of stretch film production means that manufacturers face several challenges in producing high-quality stretch films. These challenges include:
Consistency: To ensure that stretch films have consistent properties, manufacturers must carefully control the raw materials, extrusion, and winding processes.
Quality Control: Stretch film production requires extensive quality control measures to ensure that the final product meets the required specifications. This includes testing for properties such as tensile strength, elongation, and cling.
Environmental Concerns: The production of stretch films can have environmental impacts, such as the use of non-renewable resources and the generation of waste. To address these concerns, manufacturers are increasingly turning to sustainable raw materials and production methods.
Cost: The production of high-quality stretch films can be expensive due to the complexity of the process and the cost of raw materials. Manufacturers must balance the need for quality with the need for cost-effectiveness to remain competitive in the market.
In conclusion, Vivopack® stretch film production is a complex process that requires expertise and precision to produce high-quality films. The selection of raw materials, extrusion, and winding processes must be carefully controlled to ensure that the final product meets the required specifications. Moreover, several challenges in producing high-quality stretch films are faced, including consistency, quality control, environmental concerns, and cost. By addressing these challenges we can ensure that the stretch films in our offer meet the needs of our customers while also maintaining a sustainable and competitive business.